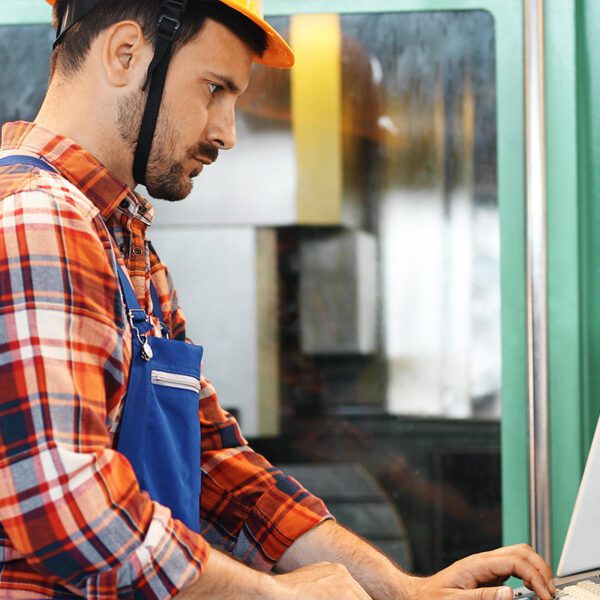
Start saving today
Whether you want to save on energy or avoid maintenance, we can show you how our smart monitoring solution will benefit your plant. Don’t wait any longer and start saving on time and costs right away.
Request a demoIn today’s manufacturing world, every euro counts. You’re already keeping a close eye on your utility bills, but what if we told you there’s often significant energy waste hiding in plain sight, quietly eating into your profits? These aren’t always obvious leaks or breakdowns; they’re the subtle, continuous drains that add up to a surprising amount over time.
For plant, production, and maintenance managers, finding these hidden culprits can feel like searching for a needle in a haystack. But with the right tools, you can pinpoint them and turn that wasted energy into real savings. Let’s look at five common hidden culprits and how smart monitoring makes them visible.
You wouldn’t leave the lights on in an empty room, right? Yet, many industrial facilities have machines running in “standby” mode long after production stops. Think of pumps, compressors, or even HVAC systems that hum along through lunch breaks, night shifts, or weekends. These “phantom loads” aren’t actively working, but they’re still drawing power and costing you money.
Why it’s hidden: It’s easy to overlook because the machine isn’t “on” in the traditional sense, or its consumption seems small individually.
How smart monitoring helps: Real-time energy monitoring reveals these patterns. You can instantly see which machines are consuming power outside of operational hours, allowing you to implement stricter shutdown protocols or automate power-offs. Our data often shows that standby consumption is one of the largest, yet easiest, areas for our clients to cut waste.
Compressed air is often called the “fourth utility” in manufacturing, and it’s notoriously expensive. Even tiny leaks in your compressed air lines force your compressors to work harder and longer to maintain pressure. This isn’t just about the air escaping; it’s about the massive amount of electricity used to generate that air.
Why it’s hidden: In a noisy factory, a small leak can be impossible to hear. Many leaks are also in hard-to-reach places.
How smart monitoring helps: While you won’t “see” the air leak, your energy data will tell the story. Smart monitors detect erratic energy spikes or continuous power draw from your compressors even when demand is low. These tell-tale patterns signal a pressure drop from a leak, prompting you to investigate. Our system can flag these discrepancies, alerting you to leaks you might never have noticed otherwise.
Motors are the workhorses of any factory, but are they working efficiently? An oversized motor running at a low load, or an older, less efficient motor still in service, can consume far more energy than necessary for the task at hand. Degraded motors also become less efficient over time.
Why it’s hidden: The motor is doing its job, so you might not question its efficiency unless it breaks down.
How smart monitoring helps: Energy monitoring baselines your motors’ normal consumption. If a motor starts drawing more power than usual for the same output, or if you identify motors consuming excessive energy compared to similar units, it’s a red flag. This data helps identify candidates for upgrades, maintenance, or the installation of variable speed drives (VSDs) that can significantly cut consumption.
Do you have clear rules for when certain equipment should run? Sometimes, machinery or ancillary equipment runs outside of standard operating procedures. This could be a cooling system left on overnight when it’s not needed, or a conveyor running even when the main production line is idle.
Why it’s hidden: It requires constant human oversight or a perfect understanding of complex, interconnected processes.
How smart monitoring helps: By monitoring individual machines, you gain visibility into their true operational schedules. Anomalies where equipment runs when it shouldn’t – for example, machine Y stays on for an hour after machine X (which it depends on) shuts down – become immediately visible. This helps you enforce energy-saving protocols and ensure your equipment aligns with production needs.
In environments with heating or cooling demands, inefficient insulation in pipes, ovens, boilers, or even the building itself can lead to significant energy waste. Your equipment has to work harder and consume more energy just to maintain desired temperatures.
Why it’s hidden: Unless you’re doing regular thermal imaging, heat loss isn’t always obvious.
How smart monitoring helps: While not directly measuring heat loss, energy monitoring can flag an unexpected increase in the energy consumption of your heating or cooling systems. If your boiler is suddenly consuming more power to maintain the same temperature without a change in production or external weather, it signals an underlying efficiency issue, potentially due to poor insulation that needs attention.
Finding these hidden energy culprits isn’t about guesswork; it’s about having the right data. Smart energy monitoring gives you the precise, real-time insights you need to pinpoint waste, make confident decisions, and transform those invisible drains into real, measurable savings for your operation.
Ready to uncover significant savings and boost your factory’s efficiency? Let us show you how our smart energy monitoring system can reveal your hidden waste culprits and help you build a more sustainable, profitable future.
Whether you want to save on energy or avoid maintenance, we can show you how our smart monitoring solution will benefit your plant. Don’t wait any longer and start saving on time and costs right away.
Request a demo