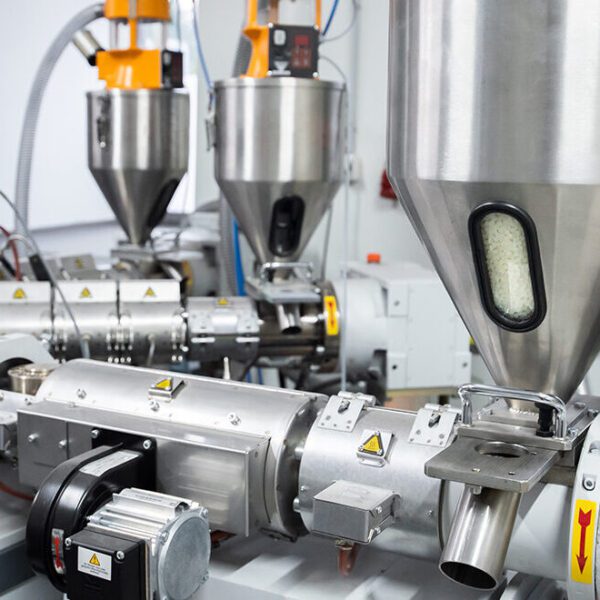
Start saving today
Whether you want to save on energy or avoid maintenance, we can show you how our smart monitoring solution will benefit your plant. Don’t wait any longer and start saving on time and costs right away.
Request a demoUnplanned downtime. Just the phrase itself can send shivers down the spine of any plant manager or maintenance professional. Lost production, rushed repairs, and budget overruns are just some of the consequences. But what if you could see these failures coming? Often, your equipment gives warning signs before it completely breaks down. Being able to recognize these signs is crucial for implementing preventative measures and avoiding costly downtime.
This blog will outline five common indicators of impending equipment failure and explore how predictive maintenance can help you keep your operations running smoothly.
Changes in the sounds or vibrations coming from your machinery are often the first clue something is wrong. A grinding noise could indicate a bearing is failing, while excessive vibration might point to misalignment or imbalance. Don’t ignore these subtle shifts – investigate them immediately. This could save you from a catastrophic equipment failure.
Whether it’s oil, coolant, or hydraulic fluid, leaks are a clear sign of trouble. They can indicate worn seals, damaged hoses, or even cracks in components. Addressing these leaks promptly can prevent further damage and potential safety hazards. Ignoring leaks can lead to increased maintenance costs and production downtime.
Equipment operating at higher-than-normal temperatures is a major red flag. It could be due to anything from inadequate lubrication to a failing cooling system. Continued operation under these conditions can lead to rapid wear and catastrophic failure. Prevent equipment overheating by implementing regular inspections and maintenance schedules.
Have you noticed a decrease in your equipment’s output or efficiency? Is it taking longer to complete tasks, or are the results less consistent? These subtle changes in performance can signal underlying issues that need attention. Optimize equipment performance through preventative maintenance and timely repairs.
Burning smells, electrical odors, or other unusual scents emanating from your equipment should never be ignored. They can indicate electrical faults, overheating components, or other serious problems. Shut down the equipment immediately and investigate the source of the smell. Prevent electrical fires and other safety hazards by addressing unusual smells immediately.
Reactive maintenance, where you only fix equipment after it breaks down, is costly and disruptive. Predictive maintenance, on the other hand, uses data and analytics to anticipate potential problems before they occur. By implementing predictive maintenance strategies, you can:
Modern technology makes predictive maintenance easier than ever. Sensors can monitor various parameters like vibration, temperature, and oil quality, providing real-time data on equipment health. This data can be analyzed to identify trends and predict potential failures. By leveraging these tools and techniques, you can shift from reactive to proactive maintenance, keeping your equipment running smoothly and your operations profitable.
Whether you want to save on energy or avoid maintenance, we can show you how our smart monitoring solution will benefit your plant. Don’t wait any longer and start saving on time and costs right away.
Request a demo