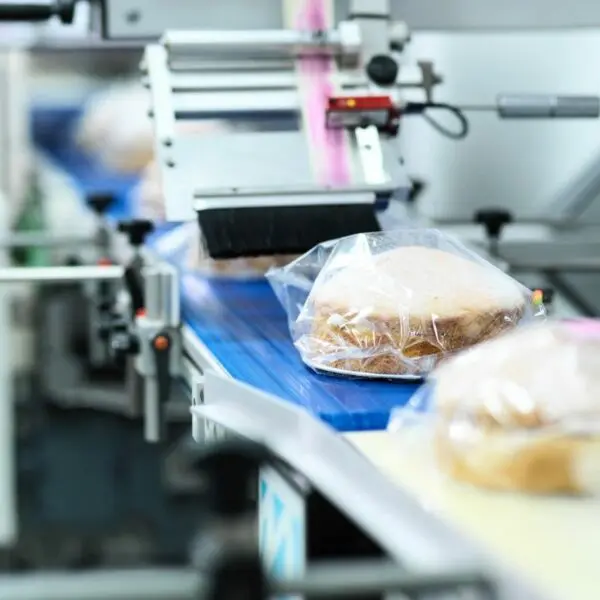
Start saving today
Whether you want to save on energy or avoid maintenance, we can show you how our smart monitoring solution will benefit your plant. Don’t wait any longer and start saving on time and costs right away.
Request a demoOEE (Overall Equipment Effectiveness) measures how well manufacturing equipment is utilized by combining availability, performance, and quality metrics into a single efficiency score.
This guide will walk you through the process of calculating OEE, explaining each component in detail and providing practical tips to ensure accurate measurement. By the end, you’ll have a solid understanding of how to apply OEE in your manufacturing operations.
OEE measures manufacturing effectiveness by evaluating three components: Availability, Performance, and Quality.
Together, these components help you identify inefficiencies and improvement areas in your production process.
Calculating OEE involves measuring each of the three components and then combining them to obtain an overall OEE score. Here’s a step-by-step guide to help you through the process:
To calculate Availability, you first need to determine the planned production time and the actual operating time.
Availability = (Operating Time / Planned Production Time) × 100
Example: If the planned production time is 8 hours (480 minutes), but the machine was only running for 7 hours (420 minutes) due to a breakdown, the Availability would be:
Availability = (420 minutes / 480 minutes) × 100 = 87.5%
Performance is calculated by comparing the ideal cycle time to the actual cycle time for the total number of units produced.
The formula for Performance is:
Performance = ( (Ideal Cycle Time × Total Units Produced) / Operating Time) × 100
Example: If the ideal cycle time is 1 minute per unit and 400 units are produced in 420 minutes, the Performance would be:
Performance = ((1 minute/unit×400 units) / 420 minutes) × 100 = 95.2%
Quality is calculated by determining the number of good units produced versus the total number of units produced.
The formula for Quality is:
Quality = (Good Units / Total Units Produced) × 100
Example: If 390 out of 400 units are produced without defects, the Quality would be:
Quality = (390 good units / 400 produced) × 100 = 97.5%
Finally, to calculate the OEE score, you multiply the three components—Availability, Performance, and Quality:
OEE = Availability × Performance × Quality
Example: Using the values calculated above:
OEE= 87.5 × 95.2 × 97.5 = 81.2%
An OEE score of 81.2% indicates that the manufacturing process is operating at 81.2% of its full potential.
A good OEE score depends on several factors, including the industry, the type of manufacturing process, and specific operational goals. OEE scores can vary widely depending on these factors. For example, industries with highly automated processes may achieve higher OEE scores, while those with more manual operations might see lower scores. It’s important to understand these variations when assessing your own OEE performance.
Here’s a general breakdown of OEE scores:
Below 60% | Poor |
Indicates significant inefficiencies, with major issues in availability, performance, or quality. | |
60-70% | Fair |
Common in many manufacturing environments but shows room for improvement in multiple areas. | |
70-85% | Good |
Reflects a well-optimized process with some minor areas for improvement. | |
Above 85% | Excellent |
Considered world-class performance, with minimal downtime, high production speed, and low defect rates. |
Understanding where your OEE score falls on this scale can help you identify areas for improvement and set realistic goals.
Accurately calculating OEE requires reliable data collection and careful analysis. Here are some practical tips to ensure you get the most accurate OEE measurements:
Consistency and accuracy are key. Use standardized methods and consider automated monitoring tools to minimize human error and capture real-time data.
Watch out for frequent mistakes like incorrect calculations or misinterpreting results. Ensure that everyone involved understands the data collection process and its importance for accurate OEE measurement.
OEE is more than just a performance metric; it’s a valuable diagnostic tool. Use it to identify and prioritize areas for improvement. Regularly review OEE scores, and investigate significant changes to uncover root causes.
While the basic calculation of OEE is straightforward, advanced manufacturing environments may require additional considerations:
Different manufacturing processes, such as batch production versus continuous production, may require adjustments to the OEE calculation. Tailor your approach to fit the specific context of your operations.
Consider how to account for scheduled maintenance, changeovers, and other planned downtime in your OEE calculation. This will help you get a more accurate picture of your actual production efficiency.
Set realistic OEE targets and compare scores across machines, shifts, production lines, or plants to gain valuable insights into your operational performance. Low scores will serve as a starting point for investigation, helping you identify root causes of inefficiencies. Use benchmarking to pinpoint areas that need the most improvement and establish goals for continuous enhancement.
Using OEE monitoring software can make calculating and tracking OEE much easier. This software automates data collection and analysis, giving you real-time insights. It also reduces the risk of human error, so you can focus on improving your processes.
To learn more about how OEE software can benefit your business, check out our blog on OEE software. Sensorfact offers smart monitoring solutions that simplify OEE tracking and help you achieve better operational performance.
Read more about our OEE solutionWhether you want to save on energy or avoid maintenance, we can show you how our smart monitoring solution will benefit your plant. Don’t wait any longer and start saving on time and costs right away.
Request a demo