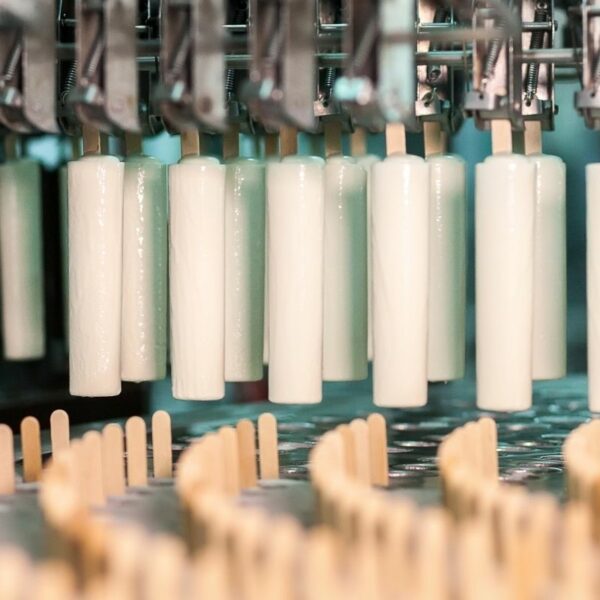
Start saving today
Whether you want to save on energy or avoid maintenance, we can show you how our smart monitoring solution will benefit your plant. Don’t wait any longer and start saving on time and costs right away.
Request a demoEfficiency and productivity have always been top priorities for manufacturing companies that strive to streamline operations, reduce waste, and improve product quality. A crucial metric for measuring efficiency is Overall Equipment Effectiveness (OEE).
OEE shows you how well a manufacturing process performs compared to its full potential. By tracking OEE, you can identify inefficiencies, spot areas for improvement, and make better decisions to enhance performance. In this blog, we’ll cover what OEE is, how it’s calculated, and why it’s important for manufacturing success.
OEE is a comprehensive metric that measures the effectiveness of manufacturing operations. It is designed to provide a clear picture of how well production equipment is being used by considering three critical components: Availability, Performance, and Quality.
This component measures the proportion of planned production time that the equipment is actually operating. It accounts for any unplanned downtime, such as equipment breakdowns or delays, that can reduce the overall effectiveness of the manufacturing process.
Performance evaluates the speed at which the production process operates compared to its designed or ideal speed. It considers factors like slow cycles and minor stoppages, which can hinder the manufacturing process from reaching its full potential.
The quality component measures the proportion of good products produced without defects. It accounts for any rejects or rework that occur during production, which directly impacts the overall efficiency and output quality.
By analyzing these three components, OEE provides a detailed understanding of where inefficiencies might exist in the production process and highlights opportunities for improvement.
The OEE formula is straightforward yet powerful:
OEE = Availability × Performance × Quality
Each component is expressed as a percentage, and when multiplied together, they yield the OEE score, which is also represented as a percentage. For example, if a manufacturing process has 90% Availability, 95% Performance, and 98% Quality, the OEE would be:
OEE = 0.90 × 0.95 × 0.98 = 0.8379 or 83.79%
This score indicates that the manufacturing process is operating at 83.79% of its full potential. For a more in-depth exploration of how to calculate and interpret OEE scores, read our detailed blog on OEE calculations.
OEE is a powerful tool, offering insights that drive continuous improvement and operational excellence. Here’s why OEE is so important:
OEE helps you to pinpoint inefficiencies in your production processes. Whether it’s reducing unplanned downtime, optimizing production speeds, or improving product quality, OEE provides a clear starting point for making improvements. It also plays a crucial role in continuous improvement strategies like Lean and Six Sigma, which aim to enhance overall operational efficiency.
By improving OEE, you can significantly reduce downtime, optimize machine utilization, and increase product quality. This leads to a more efficient production process, resulting in cost savings and higher profitability. Companies that successfully improve their OEE often experience faster lead times, reduced waste, and enhanced customer satisfaction.
In today’s competitive market, maintaining a high OEE is crucial for staying ahead of the competition. A higher OEE means lower production costs, faster response times, and better product quality, all of which contribute to a stronger market position.
Additionally, by minimizing waste and energy consumption, a high OEE supports sustainability efforts, which are increasingly important in the industry.
While OEE is a valuable metric, it comes with its own challenges and limitations. Here are some common challenges you may encounter:
Accurately collecting and analyzing data for OEE calculation can be challenging. You may struggle with ensuring consistent and reliable data, especially in complex operations with multiple variables. This issue can be easily tackled by finding the right OEE monitoring solution. The critical factors for finding the right solution are discussed in our blog about OEE software.
OEE primarily focuses on equipment efficiency and may not fully capture the overall business impact or the entire production process. It’s important to use OEE in conjunction with other key performance indicators (KPIs) to gain a holistic view of their operations.
By understanding and optimizing OEE, you can boost operational efficiency, reduce costs, and stay competitive in the market. However, it’s important to use OEE as part of a broader strategy for continuous improvement.
Looking to enhance your overall operational performance? Explore our easy-to-install OEE solution that delivers the insights you need to drive meaningful improvements.
Whether you want to save on energy or avoid maintenance, we can show you how our smart monitoring solution will benefit your plant. Don’t wait any longer and start saving on time and costs right away.
Request a demo